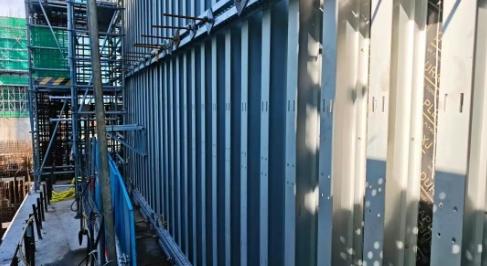
陆丰核电1、2号机组核岛的辅助厂房和附属厂房墙体尺寸大,覆盖面积广,在厂房墙体混凝土浇筑中,传统的常规大模板存在诸多局限性,主要有四大痛点:
未设置起重吊点,吊装困难且不安全。
上海油压工作室未设置加固平台,模板加固需配合脚手架平台,投入人工较多且工序复杂。
拉杆数量多,增加预埋拉杆孔的同时,也增加了材料用量,增加施工成本。
上海油压工作室面积较小,对于大方量混凝土投入模板量及人工较多。
为将陆丰核电项目打造成为精品工程、标杆工程,项目管理团队深入践行“严慎细实”工作作风,大力弘扬“陆核精神”,坚持“三个围绕”价值导向,分机组、分领域、分层级持续推进“五化”建设走深走实。按照“应模尽模、能模尽模、宜模则模、未模创模”原则,项目管理团队联合上海核工院、中核二二陆丰核电项目部,在前序项目8大类26项模块化施工经验的基础上持续开展模块化。此次投入使用的直行墙大模板正是施工工艺模块化建设内容之一。相较于常规大模板,直行墙大模板具有安全性、经济性和实用性三大优势。
01安全性设计与加固措施方面
直行墙大模板通过多维度优化确保施工安全可靠。模板增设经结构强度、材料性能及防滑设计专项优化的专业起重吊装吊钩,可安全承载模板重量,实现稳定起吊与悬挂,降低吊装隐患。加固采用M17高强拉杆自下而上进行,先在地面完成第一层、第二层高强拉杆安装固定,再于模板结构上架设三角挂凳,并通过螺栓将折叠平台与大模板体系牢固连接。模板顶口与底口配备集成装置增强整体性,底部三角架开设直径22mm孔洞并焊接M20螺母,与斜撑销轴精准连接固定,提升整体稳定性。此外,大模板重复使用率高,能显著降低材料损耗与人工成本,同时配套完善的安全防护措施与稳固支撑体系,可有效规避模板拆除过程中的安全事故,确保拆除作业安全有序开展。
02经济性方面
上海油压工作室陆丰核电1、2机组应用的4880*5800*18规格大模板体系优势显著。该体系凭借标准化大尺寸设计,大幅压缩材料拼装耗时达50%,有效提升施工效率;同时,其良好的整体性减少了生产过程中的材料损耗,实现施工成本的降低。在龙骨与支撑结构设计上,大模板横向配置3道双14槽钢龙骨,竖向采用间距300的H20铝工字梁。经严谨力学计算验证,3道双14槽钢龙骨即可满足受力需求,相比传统方案有效减少槽钢用量,简化拼装流程;而H20铝工字梁的应用,不仅增强了大模板体系的安全性,更显著提升其整体刚度与稳定性,在保障工程质量的同时,实现了材料成本与施工难度的双重优化。
03实用性方面
大模板凭借精密的支撑与紧固系统,可高效抵御新浇混凝土产生的侧压力,显著降低模板变形、鼓胀风险。相较于小块散拼模板,大模板大幅减少接缝数量,经特殊设计与处理后,能有效防止漏浆问题,确保浇筑出的混凝土墙面平整光洁,完全契合核电工程对高品质混凝土外观的严苛标准。在项目施工过程中,少拉杆设计大幅缩短施工周期;上部操作平台的创新设置,既减少了脚手架搭设量,又避免了交叉作业干扰,显著提升结构施工质量、精度与效率,同步强化作业安全性,为混凝土振捣作业提供了便捷、高效的操作空间。
在编制施工方案阶段,陆丰核电项目管理团队便对现场大模板支设工况进行深度调研与系统性规划。通过精准设计与精细化制造流程,定制的直行墙大模板在生产环节实现了高度一致性与施工精度保障。此外,大模板系统依托标准化、模块化设计理念,显著简化了施工过程中的组织管理与多方协调工作,不仅大幅提升项目管理效能、有效缩短施工周期,还通过优化资源配置降低了综合成本,实现施工效率与经济效益的双重提升。